- ONERA
- Research - Aeronautics Space Defense
- Scientific Domains
Materials and Structures
The MAS Scientific Domain
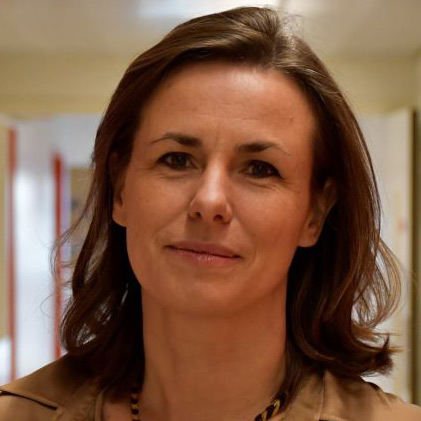
Anne Tanguy
Scientific director
of the Materials and Structures domain
Recent developments

Best Paper Award EREA 2021 – ONERA co-authors paper on structural dynamics
EREA, the association of European Research Establishments in Aeronautics, awards annually the best scientific paper of its scope. In 2021, Dimitri Goutaudier (ONERA/DMAS), Didier Gendre (Airbus), Véronique Kehr-Candillea (DMAS) and Roger Ohayon (CNAM) were distinguished among 22 nominees for their work in the field of "Long-range impact localization with a frequency domain triangulation technique: Application to a large aircraft composite panel".
Ref: Composite Structures Volume 238, 15 April 2020, 111973 https://doi.org/10.1016/j.compstruct.2020.111973

The ESCALE platform, started in 2014, collects all numerical developments in the field of test-model-calculation dialogue in order to facilitate design of materials and structures. A consortium agreement has been set up to disseminate the software and libraries in the scientific laboratories. The partners are: GeM (Nantes), Institut Clément Ader (Toulouse), LaMcube (Lille), CEA (Saclay) and Arts et Métiers (Aix en Provence). Sylvia Feld-Payet @ onera.fr

OP2i MATRIX, high temperature sintering at the best world level
The OP2i MATRIX investment operation has provided ONERA with two high-temperature sintering facilities at the highest level in the world. First one is a high-capacity DCS/SPS (Direct Current Sintering/Spark Plasma Sintering) (2500°C, 250 t, diam 300 mm), and the second one is a HIP (Hot Isostatic Pressing) than can reach temperatures and pressures up to 2000°C and 4000 bar (diam 150 mm x h 250 mm). Few facilities allow the design of refractory ceramic or metallic materials or demonstrators reaching such high temperatures on such large dimensions Aurélie Jankowiak, Johan Petit @ onera.fr
Picture: 150 mm diameter plates manufactured by DCS/SPS

MOSTRA, the latest generation of TEM microscopy at ONERA
The MOSTRA project, granted by ONERA and SESAME, will enable the development of an advanced transmission electron microscope to, among other innovations, link HR imaging to local physical properties of a wide range of materials of interest for the Aeronautic Space and Defence industrial areas (from turbine blades to nanoparticles). The partners of the project are CNRS, GEMaC (Versailles) and UMPHY (Palaiseau). Frédéric Frossard, Annick Loiseau @ onera.fr
Picture: Dielectric response of the hexagonal structure of boron nitride
MAS in brief
The Materials and Structures domain covers all the research and development activities aimed at the use of materials and structures in the aerospace and defence fields. It brings together the activities traditionally associated with Materials Science and Solid and Structural Mechanics, as well as Aeroelasticity, in a transdisciplinary approach to rely on an effective coupling between scales (from the atomic scale to the scale of the aircraft). The activities are cross-functional to three departments (DMAS - Materials and Structures, DMPE - Multiphysics for Energetics, DAAA - Aerodynamics, Aeroelasticity, Acoustics).
A major challenge is the control of the mechanical behaviour throughout the life of materials, components and structures in their environment, taking into account the complex service loads (mechanical, thermal and irradiation) which are imposed to them. For this, materials are studied and formulated at the scale of aerospace substructures or even complete structures (helicopters, airplanes, launchers...) in realistic conditions (thermo-mechanical couplings) at different scales taking into account progressive damage until the failure of the structure. To this end, the multiphysics environment must be considered with accuracy, based on experimentation and observation of the phenomena involved at the material and structural levels. This approach is critical to meet the challenge of energy efficiency of aerospace structures. Multifunctional materials are also part of the research fields of the MAS domain.
The scientific approach developed within the MAS domain relies consistently on the coupling between scales: from the finest scales in order to understand the elementary mechanisms at stake and to identify the key models and parameters, or even to guide the choice of manufacturing processes, up to the scale of structural assemblies representing aerospace vehicles. The approaches of change of scale, observation and characterization at each level play an essential role.
The development of new materials, enhanced by numerical approaches, in conjunction with experimental elaborations, and the formulation of constitutive equations including damage until failure for their industrial use (e.g., aging, damage, fatigue life, fracture and impact) are among the research areas at ONERA. They must be closely associated with the development of observation methods at increasingly fine scales and the development of Structural Health Monitoring (SHM) or non-destructive control of manufacturing processes.
The use of these materials by the industry in optimized complex structures, subjected to extremely severe operating environments for some applications, with ever-increasing safety, reliability or certification requirements, opens up a final field of research concerning the structuraldesign. Couplings with aerodynamics, thermal or electromagnetism (lightning strikes, stealth) must be taken into account in the modelling, the numerical simulation using high performance computing solvers and hardwares and of course, experimentation at significant scales. The dialogue between tests and calculations is obviously the strong research activity in this approach.
Scientific officers
MAS Themes
The research topics of the MAS scientific domain are mainly conducted by the Materials and Structures department (DMAS). Two research topics, of the Multi-Physics department for Energy (DMPE) and the Aerodynamics, Aeroelasticity, Acoustics department (DAAA) are also covered by the domain.
- Low dimension structures DMAS
- Physics and behavior of materials: from the atom to the microstructure DMAS
- Innovative structural materials DMAS
- Architectured and multifunctional materials DMAS
- Multi-scale and multi-physics modelling and characterization of materials DMAS
- Modeling of complex macroscopic phenomena (damage, fatigue, cracking and failure) DMAS
- Structural mechanics, design and optimization of structuress DMAS
- Aéroelasticity DMAS
- Numerical methods >> See the Advanced Numerical Simulation domain SNA
Low dimension structures
DMAS Annick Loiseau, Hakim Amara (@ onera.fr)
This scientific area concerns the synthesis and growth of nanomaterials (0D, 1D, 2D), structural and spectroscopic properties (dielectric, excitonic, plasmonic), experimental developments at very small scales such as TEM/EELS, photoluminescence, CVD, and finally modelling at atomic and subatomic scales, such as DFT, tight-binding models, molecular dynamics and Monte Carlo simulations.
The scientific activity involves two main research axes:
- synthesis and growth of nanomaterials
- structural and spectroscopic properties
Examples

[Synthesis and growth of nanomaterials]
Transmission electron microscopy characterization of nano-objects

[Synthesis and growth of nanomaterials]
Growth mechanism of carbon nanotubes: electron microscopy observation and Monte Carlo calculations

[Structural and spectroscopic properties]
Maps of energy losses at 8 and 12 eV in a hexagonal boron nitride crystal in the reciprocal plane normal to the stacking axis, and corresponding ab initio numerical simulations
Physics and behavior of materials: from the atom to the microstructure
DMAS Alphonse Finel, Mickael Perrut (@ onera.fr)
The objective of this scientific area is to provide constitutive equations of materials by developing models formulated at the necessary time and space scales depending on the underlying processes. The approach is therefore necessarily multi-scale and, at the final scale of the microstructure, multi-physical.
The scientific activity involves the following research axes:
- Physics of microstructures: atomic and continuous scales
- Physics of plasticity: discrete dislocations and density models
- Transport mechanisms in materials (electrons, phonons)
- Thermodynamics and kinetics of multi-constituted alloys
Examples

Phase Field Method The phase field method is a continuous theory. Its numerical implementation requires a sufficiently fine discretization of the interfaces, represented by the spatial variations of the fields. A new formulation, called SPFM - Sharp Phase Field Method -, in which the interfaces are resolved with a single point without generating friction on the grid has been proposed, which significantly increases the numerical capabilities of the method (Fig. 1 b)..

FFT mechanical solvers SPFM is based on an abrupt description of the interfaces, as they are resolved in a single grid point. The coupling of the method with mechanical fields (elastic and plastic) therefore requires the development of a mechanical solver able to handle strong heterogeneities (elastic constants, eigenstrain tensors). We have developed such a solver, that is intrinsically discrete, using an FFT approach. This solver is very stable for any contrast, unlike classical continuous solvers. It is also very efficient from a numerical point of view. The mechanical equilibrium of a composite described by about 50 million degrees of freedom requires about 2000 s single processor (see figure).
Innovative structural materials
DMAS Cécile Davoine, Aurélie Jankowiak (@ onera.fr)
This topic brings together research activities concerning the development of metallic, ceramic and composite materials. The goal is to provide a gain in terms of durability and/or lightening of structures, aiming at higher operating temperatures while favouring a low environmental impact. The activity is also related to the analysis of the relations between the elaboration process, the microstructures and the associated properties (mechanical and others). This work is based on ONERA expertise available in the DMAS in transformation techniques, mechanical and microstructural characterization.
The scientific activity involves the main research axes:
- Development of metallic alloys
- Development of new ceramic and composite materials
- Development of protective and repair coatings
- Development of methods for monitoring and controlling material health
Architectured and multifunctional materials
DMAS Marc Thomas, Florence Saffar (@ onera.fr)
This scientific area involves all the research activities related to architectural, functional and multifunctional materials. It concerns the studies related to material elaboration and in particular of the additive manufacturing processes, and the means of characterization associated with the desired functionality. The objective is to develop multifunctional materials with mechanical (impact, vibration, super elasticity), acoustic, thermal, optical, aerothermal, or gradient properties.
As far as the DMAS department is concerned, the scientific activity involves the following research axes:
- Thermal Barriers and multilayer systems: this axis takes into account the problems related to the system made of superalloys, sublayers and ceramics
- Materials obtained by Additive Manufacturing (AM): this axis includes transpiring and aspiring wall materials, architectural materials and property gradient materials
- Functional materials: this axis includes functional ceramics, energy absorbing materials and compounds for non-linear optics
Multi-scale and multi-physics modeling and characterization of materials
DMAS Anna Ask, Louise Toualbi (@ onera.fr)
This scientific area concerns i) the modeling of the multi-scale behaviour of materials, ii) the modeling of processes and their impact on the macroscopic mechanical behaviour and iii) the multi-physics modeling of materials and their degradation in complex environments.
The development of models that account for the macroscopic behavior (static, transient dynamic and fatigue) from the evolution of the microstructure is an important scientific issue of these activities. By improving these models with multi-physical components (diffusion, thermal, thermochemical, electrostatics, ...), it is possible to account for the influence of processes or environment (oxidants, icing, fire, lightning ...) on the performance of materials and structures. The validation of these models is based on original and specific experimental developments.
The scientific activity involves the following research axes:
- modeling of the materials behavior
- modeling of processes
- multi-physics modeling of the materials degradation
Examples

Dynamic phase-field simulation Dynamic phase-field simulation, at the microstructure scale, of the transverse fracture of a ceramic matrix composite (CMC). This type of simulation should allow understanding the role played by material elaboration parameters (spacing between fibers, tenacity of the fiber coating, etc.) on its macroscopic response. A domain decomposition approach (FETI method) was applied to the resolution by coupling solvers using 2x40 cores to model this structure with a very high mesh size (9 million unknowns).
Contacts : Johann Rannou, Christophe Bovet (@ onera.fr)
Modeling of complex macroscopic phenomena (damage, fatigue, cracks and failure)
DMAS Myriam Kaminski, Martin Hirsekorn (@ onera.fr)
This scientific area deals with the modelling of macroscopic phenomena that are critical to design innovative and competitive structures. In particular, it concerns damage and cracks models based on a detailed description of the mechanisms, in relation with the previous scientific area. The area implies a strong coupling between the damage modelling and the underlying experimental activities, including non-destructive testing for the prediction of the defects tolerance.
The scientific activity involves the following research axes:
- damage and life prediction
- prediction of failure and description of crack path under static/dynamic/cyclic loading conditions
- detection and monitoring of damage
Examples
Identification of a crystalline plasticity model by combining image correlation and EBSD mapping to model the ductile fracture of AA2139 aluminum, then comparison with tests on different specimen geometries with in situ monitoring of crack initiation mechanisms (European project Cleansky2)
Structural mechanics, design and optimization of structures
DMAS François-Xavier Irisarri, Cédric Julien (@ onera.fr)
This scientific area covers all DMAS activities dealing with structural mechanics. It includes the analysis, design and optimization of structures, as well as their instrumentation for integrated structural health control purposes.
The scientific activity involves the following research axes:
- design of structures and their optimization
- modelling the response of structures subjected to external loads such as impact or crash
- vibrational analysis
- integrated structural health monitoring
Example

Coupled Euler/Lagrange simulation of transport aircraft ditching
Aeroelasticity
DAAA Cédric Liauzun, Cyrille Stephan (@ onera.fr)
- Aeroelasticity
- Hydroelasticity
- Vibration dynamics
- Modélisation, simulation et identification
- Prediction of performance, stability (flutter, LCO) and forced responses
- Prediction and lightening of static and dynamic loads
Examples

CARACAL Aeroelastic design for gust load reduction Advance expertise in optimized aeroelastic design of flexible airfoils by improving numerical simulation methodologies and tools
